Reader Suggestions
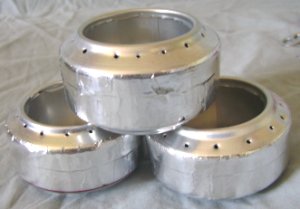
As this website gets more publicity and more people start finding it, I’ve been getting more and more suggestions for ideas on how to improve or tweak the soda can stove. Some of the ideas seem like they might have merit, but I don’t really feel comfortable officially “endorsing” any of them since I haven’t tried them. If and when I do, however, I might update other pages on this site if it turns out I really like the idea! But in case you want to see what others are suggesting, I’m starting to keep a list here of the more interesting ideas.
- Beer/Coke Bottle Hybrid Stove
- An Inner Wall Substitute
- A New Way to Light a Stove
- Unexpected Downsides of a Penny-Can Stove
- Caldera Cones and Trangia Alcohol Stoves
- Six Alcohol Fuels Directly Compared
- Getting Around the High-Temperature Tape
- A Lid For Your Stove
- The One-Can Soda Can Stove
- Another One-Tool, One-Can Soda Can Stove
- The Joys of Epoxy
- The Hammering Man
- A Better Top & Bottom Fit
- A Better Inner Wall
Do you have a suggestion? Use that Contact Us link at the bottom of the page (or the link I just provided). Perhaps I’ll add your suggestion to this list! (No promises, though, and I may not reply very quickly since this website isn’t exactly my highest priority—especially so if I’m on a thru-hike somewhere!)
A Beer/Coke Bottle Hybrid Stove
Suggested by: James "Wahoo" Milroy
Wahoo created a PDF file showing his preferred stove design: Wahoo’s Hybrid Beer/Coke Bottle Alcohol Stove. (The document will open in a new window.)
An Inner Wall Substitute
Suggested by: Wayne from Perth, Western Australia
One small departure from your instructions was to use aluminum flashing for the inner wall. It’s a bit thicker, but makes the assembly a bit easier if you are ham-fisted.
A New Way to Light a Stove
Suggested by: Pigdart
I light my stove by filling the stove as normal, then dipping my knife in the fuel in the stove and lighting the knife, the using the lit knife to light the stove. I haven’t tried this in real cold weather though.
Unexpected Downsides of a Penny-Can Stove
Suggested by: Daniel
I’ve put together a few stoves now, I started out with a few penny stoves, but recently I tried out a soda can stove very similar to the one one your page. The difference is just that i glued mine together with JB weld, and it’s also 40 mm high instead of your standard 35.
When I compared the two stoves I found that the penny stove is in fact faster to boil water. With the same pot and pot stand I had a boil time for two cups of water at about 5:20 on the penny stove and just over 7 minutes with the soda can stove. The interesting thing though is the fuel consumption. With the penny stove I got a roiling boil after 5:20, and the fire in the stove died out after approximately 6 minutes, using one ounce of fuel. In the soda can stove, however, it took 1:40 minutes longer to reach a roiling boil, but I was just using half an ounce of fuel and the stove lasted 11:45 minutes before burning out, making it nearly 4 times more fuel efficient.
I can wait two minutes extra for my meals if it means I can carry 1/4, or 1/3 of the fuel to be on the safe side.
Caldera Cones and Trangia Alcohol Stoves
Suggested by: Curtis
I use the Caldera Cone in combination with the Trangia Alcohol Stove. So far as I’m concerned this is the best combination ever invented—it’s extremely fuel efficient. Due to the high efficiency it wouldn’t surprise me if for some uses it uses less fuel than when using Coleman fuel.
With 90 milliliters of alcohol, I’m able to cook 3 cups of dry beans for over 4 hours and they become extremely tender. To get an even lower simmer, I place the Trangia alcohol stove into a water bath. My Coleman fuel stove can’t get such a low simmer which is part of the reason why this stove is more efficient.
Six Alcohol Fuels Directly Compared
Suggested by: Steve
Steve sent me a link to this YouTube video pitting six different alcohol fuels against each other in terms of cost and speed, and you can also see which fuels are sooty. I wouldn’t even suggest using a fuel that was sooty unless that’s the only option you can find. Soot is a mess to clean up!
If you want spoilers.... yellow HEET was the fastest to burn while the 91% alcohol was the cheapest. However, the 91% was very sooty and one of the slowest to burn while the yellow HEET was the second cheapest and not sooty at all so Steve declares that the overall winner.
Denatured alcohol—what I usually use—comes in the middle in terms of speed and cost.
Getting Around the High-Temperature Tape
Suggested by: Micheal
Instead of carefully measuring the height of the bottom, cut it at least 3/16" too long, assemble as directed (should mention that the inner ring is sized to the outside of the hole in the upper portion) press the upper portion tightly down against the inner ring and trim counter-clockwise (I guess if you had a left handed scissors in would be the opposite way). This leaves the edge about a 1/16" taller that the lip of the upper. Using the edge of the scissors roll this edge over the lip of the upper while pressing the upper into place firmly (the motion is not unlike peeling a potato). This will hold the two pieces together very firmly. Repeat this procedure to the rough edge of the hole in the inner ring and this will both smooth that edge and press the upper firmly to the inner ring. Rolling these to edges removes the shape edges and eliminates the need for the heat tape, which is rather expensive to buy a roll just to use a small strip. This method produces an extremely robust fit with absolutely no extra cost.
A Lid For Your Stove
Suggested by: Jesse
I built a stove and noticed that the main opening was still lit when in use. I don’t have much experience with these types of stoves so I may be wrong. About 10 minutes of scouring and etching the outside lip of a spare pop can with a knife, I made a lid for the stove while in operation. I used something to prod it in place when the jets kicked in.
My guess is that this will add to the burn time by not letting the alcohol vapors be ignited and wasted via the main opening reservoir. I hadn’t done much testing with this yet but it did seem to lengthen the burn time. Also, to make it better fit, I rubbed the lid on the main opening for a few minutes. Please let me know if this helps lengthen the burn time!
My note: I don’t know—I’ve never tried it—but it seems logical enough. You’ll definitely have to wait for the stove to warm up enough to get the jets burning well before dropping the lid into place. I’m actually a little surprised this doesn’t cause the stove to go out completely, but if it works, I’m not going to knock it! =)



The One-Can Soda Can Stove
Suggested by: Milo
I’ve looked at a bunch of YouTube videos about alcohol stoves and found a perfect one-can design almost identical to yours. Except, it takes just one can and no epoxy. Differences are, holes in the top of the can, not the bottom; thumbtack used to make 16 or 24 or 32 holes (depending on what you want); top of top is then cut out; top is cut off at 1.25"; bottom is cut off at 1"; inside cut to 1.5" from remaining can; then bottom is slipped into top. That last part is tricky but once done, hermitic seal without leakage. I made stoves from mini soda cans, regular soda cans, big beer cans. Oh, and I add a larger snuffer that goes over the entire stove; and a cut-off tin can bottom as a safety plate for cooking on flammable surfaces.
My note: I didn’t find the YouTube video that Milo describes, but I did find one by someone who not only used a single soda can to create his stove, but used nothing more than a utility knife to make it. It’s essentially the same design as here, but it just goes to show how easy these things are to build!
Another One-Tool, One-Can Soda Can Stove
Suggested by: Dominic
One person asked me about the design in this video. I haven’t tried making it myself, but it looks easy and there’s a certain elegance in its design that I find appealing. Although I haven’t tried it myself, the fact that the stove is also the pot stand makes me think it might be most suitable for boiling water rather than cooking food, kind of like the Cat Food Can Stove.
The one thing I really do like about it, though—it’s a heck of a lot easier to save any leftover fuel than the stove designs on this website!
But if you like this design, by all means, go for it! =)
The Joys of Epoxy
Suggested by: Pete
I just for the first time learned about soda can alcohol stoves from my soon to be son in law. I am fascinated by them. I use Pellegrino Orange soda cans, but it doesn’t matter...all brands seem to work. I’ve experimented with designs. At first the best length of time we could keep a stove running was between 5 and 15 (stretching it) minutes. I’ve found that because of the relatively low temperature alcohol burns (I use 90% IPA), there are some things I was able to do without worrying about the damage due to heat.
I found I could seal the bottom and top pieces together nicely by “painting” a little 5-minute setting clear epoxy around the bottom where the top “skirt” fits over the bottom piece of the can. This strengthens the whole structure and less care can be given to worrying about the two pieces (top and bottom) slipping out of line.
Then what I found helped tremendously was using the same epoxy I seal the inside joint all around the entire circumference where the inner interstitial plate fits under the lip of the top piece of the can. This seal not only strengthens the placement inner plate so it has less chance to shift by accident, but seals it so less vaporized alcohol might leak. In other words it guarantees that more of the vapor will exit the burner holes.
First the burner holes lit faster. I didn’t have to wait as long for the burner to heat up after lighting the center of the container. The flames lit up out of the burner hole much more quickly. Second I got a more controlled flame out of the burner holes. Third I got an exceptional burn time. Without sealing the top part where the interstitial fits into the lip of the top part of the can, I got at best a 15 minute burn. That was pushing it... actually the best burn time was only about 10 minutes. By sealing that joint I got a 35 minute burn time. 35 minutes! I made 12 burners in all and sealed three of them as I described. Each one burned just the same and for 35 minutes. This was a huge success.
Because of the low burn temperatures I found the flame did not adversely affect the epoxy at all. In fact it actually served to harden the epoxy better causing the burner overall to become more sturdy. I find it an amazing little device.
The Hammering Man
Suggested by: Dave
Just a suggestion about making the stove. When I made one, I took the top half of the stove and stretched the wall of it by tapping the wall with a hammer against a vice, all the way around. It made a very nice fit onto the bottom half.
A Better Top & Bottom Fit
Suggested by: Eric
To slide the top over the bottom without cutting slits in it or crumpling the bottom requires expanding the top. Unfortunately the aluminum is too work-hardened to stretch this much without splitting. I finally figured out that the solution is to anneal the top. Then it can be easily stretched over an unopened can bottom, worked off, and then slid over the bottom. To maximize the seal between the two surfaces, I made the top and bottom the same height (7/8").
Annealing sounds pretty fancy, but it’s really quite easy and quite forgiving. I held the stove top with a pair of tongs, by the lip, at the center hole. I turned up my gas stove fairly high, and held the top over the flame, moving it continuously, to evenly heat the straight wall of the can all around. I may have heated it more than necessary, but what I did was heat it until the paint on the can just started to smoke, which was probably under a minute of heating time. Then I immediately plunged the can top into a container of water to quench it.
The change in the material was striking—not quite limp but definitely soft. It was easy to press the can top over an unopened can, and it didn’t take a lot of effort (although a fair amount of care) to work it back off again. Then it was fairly easy to slide the top over the bottom as long as everything was held straight. Once I got it started, I put a thin coating of high temperature RTV around the outside of the can bottom before pressing the two halves together.
I put the burner holes in last. The softness of the annealed aluminum made this easy, but it also dimpled the stove around each hole, which doesn’t look as good. So I think the next one I make I’ll put the holes in before cutting the top to length and before annealing. [My note: I think this is probably a good idea—punching the holes first.]
When I get time to experiment, I want to see if I can partially anneal the aluminum by heating it a little less, but my attempt to find a “sweet spot” of partial annealing didn’t pan out. Either I didn’t heat it enough to soften, or I heated enough to be fully softened; there was no in between... However, I have to say that the final stove is plenty sturdy, being reinforced by the inner wall and the stove bottom.




and a few seconds more, and then... Fsssssss!

the bottom of an unopened can. I found the
best way to get it off without damaging it
was to twist it off, like unscrewing a jar lid.
I repeated this several times, going farther onto
the full can each time. Finally I put it about
halfway on again and gently rocked it slightly
flare out the open end—not even enough to be
visible, just enough make sure the stove bottom
would start smoothly into it.

the stove bottom in upside down.


the top and bottom I put a bead of
RTV all the way around the bottom
next to the top. (Feline supervision
is optional.)

the bottom with a toothpick.

it home and wiping off the excess RTV.
A Better Inner Wall
Suggested by: Eric
I constructed the inner wall out of a 5.5 oz aluminum V8 juice can.
-
File flat across the bottom of the can, rotating it continuously, until you file through the ridge and start to break through into the groove on the other side.
I’ve filed a flat across the ridge in the bottom of the can and if you look closely you can see two cracks where I’ve broken through. -
Strike the dimple in the end of the can to pop out the center, tear it out, and clean up the inner diameter of the hole with a half-round file. This end (the bottom of the can) is now the top of the inner wall, and it fits perfectly into the groove in the top of the stove.
You can see some shreds of aluminum around the hole that need to be cleaned up with the file. After I do this, this end will fit perfectly into the groove on the inside of the stove top. -
Cut the top of the can (bottom of the wall) off to the desired length (1-3/8"). Scribe a mark around the wall 1/8" from this end (1-1/4" from the top of the wall).
-
Cut three v shaped notches, about 3/16" wide, evenly spaced around the can, from the bottom of the wall to the scribed line.
-
Cut slices, about 1/4" apart, from the bottom edge of the wall up to the scribe mark, creating a series of tabs.
-
Grab one of the tabs that is next to a notch with a pair of needle-nose pliers, with the tip of the pliers at the scribed line. Twist the tab slightly to separate it from its unbent neighbor and bend it inwards slightly, and slightly away from its neighbor.
-
Repeat with the neighbor tab. The neighbor tab will now slightly overlap the first tab.
-
Repeat with each tab, working in order around the can. You will end up with the tabs slightly shingling over each other; each tab will slightly overlap a neighbor on one side and be slightly overlapped by a neighbor on the other.
Note how I’ve tried to shingle or overlap the tabs, creating a sort of “turbine” appearance. -
Test fit inner wall into the stove bottom. The tabs should slide down the groove, where they will bottom out, firmly seating and centering the inner wall.
-
At assembly, I filled the groove in the stove top with high temperature RTV to seal the inner wall to the stove top. High temperature epoxy would also work well.
The finished stove. Note how the tabbed end seats and self-centers in the groove in the stove bottom. It doesn’t form a seal, but we want fuel flow at the bottom anyway.
Notes:
-
An alternative to shingling the tabs is to replace the straight cuts with narrow V-shaped notches. That’s what I did on my first version, and it worked fine, but I didn’t think it looked as nice as the shingled version, and it required more cutting.
This is the alternate method (shown before bending). - The three notches may not be strictly necessary; there may be enough fuel flow between tabs without them. I just wanted to be sure.
That’s it!